The bottom line is that, if the parent metal is not up to the melting point of the solder then the solder will simply pool on the surface. The easiest way to ensure that the parent metal is at the melting point of the solder is to use the parent metal to heat the solder. When the solder melts then you automatically know it will readily fuse to the parent metal.
While I agree that molten solder can be used to get that heat into the parent metal, and is a technique I use myself, especially when soldering wiring, the easiest way to teach someone new to soldering and to help them avoid the frustrations that too cool a parent metal can create, is to heat the solder with the parent metal. Once they have mastered that technique they are better prepared to then go on to other techniques as described.
Going on to slightly more sophisticated techniques is going to be an easier path after a good understanding of the basics has been acheived. Consequently while I disagree with the thought that smaller jobs made of multiple joints will probably fall apart, a sound understanding of the concept of heat transfer can help you acheive some quite complex small jobs as well as making you aware of what you shouldn’t try. Using solders of different melting points is one technique but even the handrails shown here were all soft soldered in place by using the rails to heat the solder. Every joint is soldered seperately and nothing fell apart.
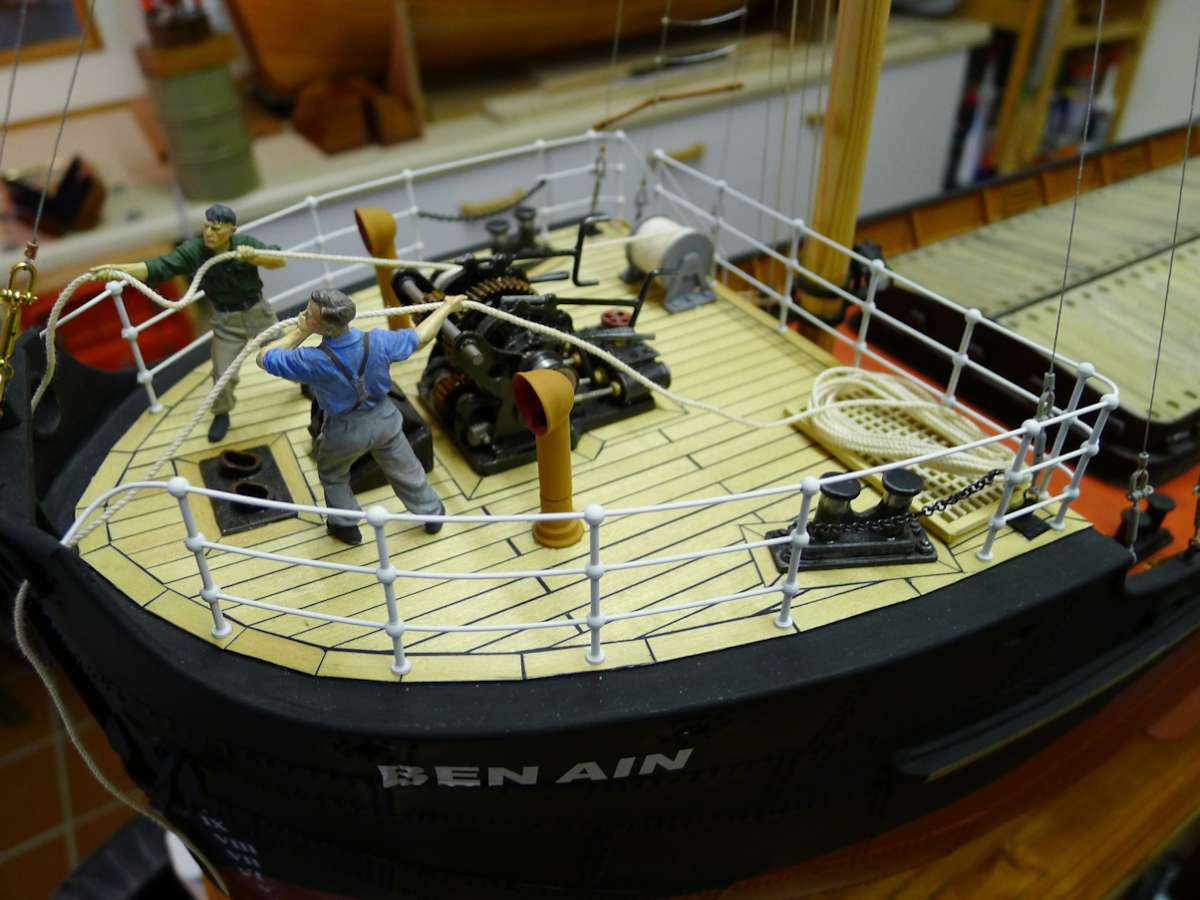
Again a good understanding of the heat flow will help when soldering two metals of very different specific heat capacities and different heat flow rates such as a thick brass bush onto a very thin tin plate. Again the best approach was to let the parent metal melt the solder as it would have been very difficult to get the temperature of the brass up without overheating the tin. The entire brass bush needed to be at a consistent temperature to ensure an even fillet of solder was created all the way around the bush and capilliary action took the solder into the joint.
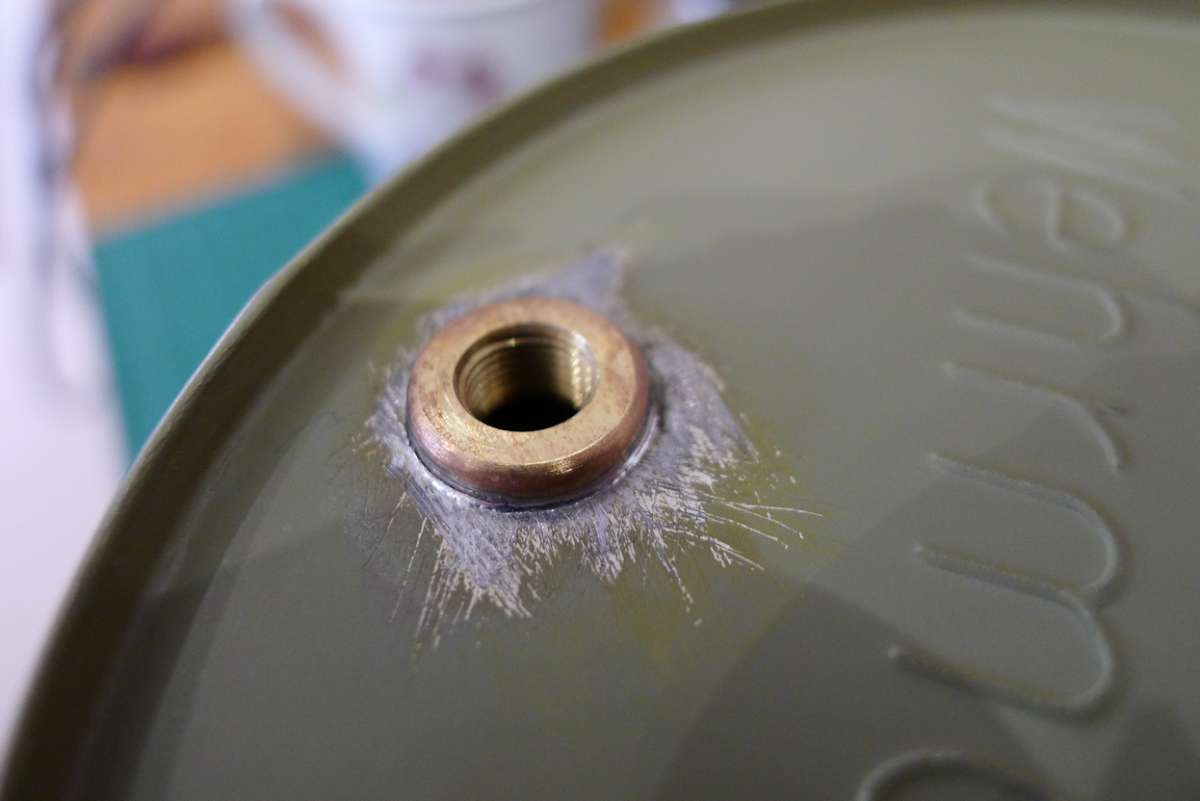