Hi Neil,
There's nothing special about the kit I use and no black art about stopping it fall apart when soldering bits close together.
None of my material – tin plate – is 'virgin'. It's just old tin cans that are cut up. Gallon cans are good because they provide large areas of ten thou plate. Smaller cans tend to be thinner and are good for 5 to 8 thou material. Some beer cans are steel and give 3 thou material. It's all a matter of the application. The sheet bits are flattened by bending and using an old rolling pin. External paint is removed with paint stripper if necessary but often I leave it in place if it's not seen or going to be soldered. Food tins used to be a good source until they started corrugating the sides. Virgin plate can be found on the web but it's a needless expense.
The flux I use is the standard grease like compound I use for domestic plumbing. The current tin is 'Telux', but 'Fluxite' is just the same. A tin will last years. I apply it with a small paint brush along the joint line.
The solder is a bobbin of 'AutoSol' 1.5mm wire. It's not cored with flux and is the standard 60/40 composition of lead and tin. Again, a large bobbin will last years. I've never tried any of the newer 'lead' free solders so can't comment.
Most of the soldering is done with a standard 'Weller' 40w iron. For larger thicker areas I use an old 'Henley Solon' 100w iron. I found the Weller tips burnt out relatively quickly and replacements hard to find or quite expensive (they are coated with a plated finish). I now make my own from a piece of 1/4 inch copper bar. They work just as well and can be easily shaped for the tip profile needed. Normally that's just a chisel end. None of the irons are temperature controlled. When solder will melt easily on the tip they are hot enough and are turned off after the job to stop oxidation.
Where the set up is delicate and touching with an iron is likely to disturb the pieces, I use a small chef's butane torch or a standard plumbers gas torch. All the bits are shown below.
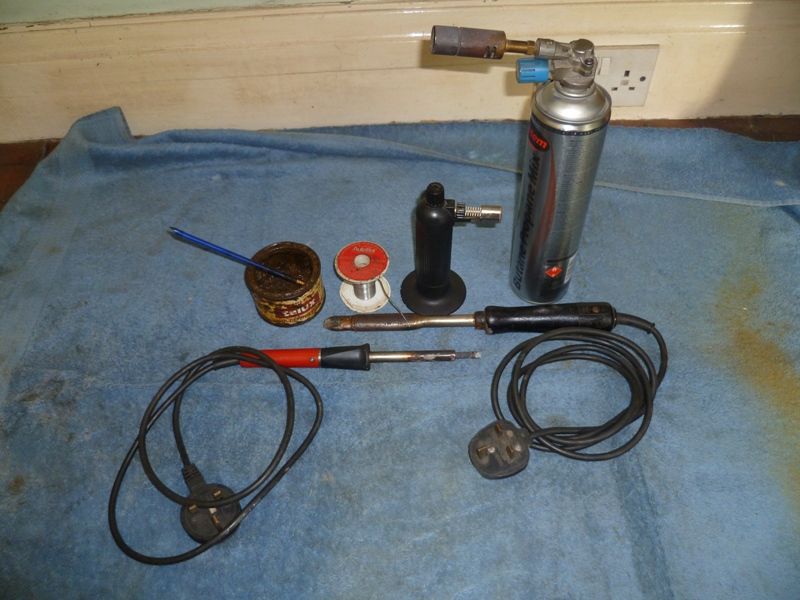
The neighbouring parts will not fall apart if the golden rules of soldering are followed. The parts should be very clean along the joint line (fine emery paper or scotch bright). The joint line should be well fluxed and close fitting. The iron should be up to temperature and well tinned. Feed solder can be added from the roll (on to the tip, not the part) or cut into small strips and laid along the joint line. If the latter is done touch the solder with the iron not the part. Heat is transferred to the part through the molten solder far quicker than hard contact between the iron and the part. Done well the solder will flash quickly into the joint long before any neighbouring joints even become warm.
Hope all this helps. It's simply my experience and might not be the best advice.
Best Regards,
Len