There seems to be some interest in big model yachts at the moment so I thought I would start a new thread to cover the build of our A class hull, Serica II. It has not yet been completed and sailed, but it has connections with some of the most famous names in UK model yachting so I will start with its history. Over the next few months I will add some more photos as the build progresses and hopefully we will have it on the water next year, about 60 years after it was originally designed.
My wife Elizabeth is an enthusiastic restorer of vintage model yachts and sailing vessels. We saw Serica II advertised in the Turning Pole, the journal of the Vintage Model Yacht Group about a year ago. Elizabeth has about 20 models ranging from a 78 inch long 10 rater down to toy Star yachts so an A class would fill the hole in her collection at the large end of the class size range. With the help of the Vintage Model Yacht Group, of which we are both members, and in particular David Bell, we have now managed to trace the history of this particular hull.
Serica was designed in 1956 by Bill Daniels for Norman Hatfield, for the princely sum of 3 guineas. Bill Daniels was one of the most influential figures in British model yachting, being an active designer, builder and competitor from around the start of the twentieth century until his death in 1959. Here is a picture, courtesy of David Bell, showing Serica (registered K750) some time in the 1950's
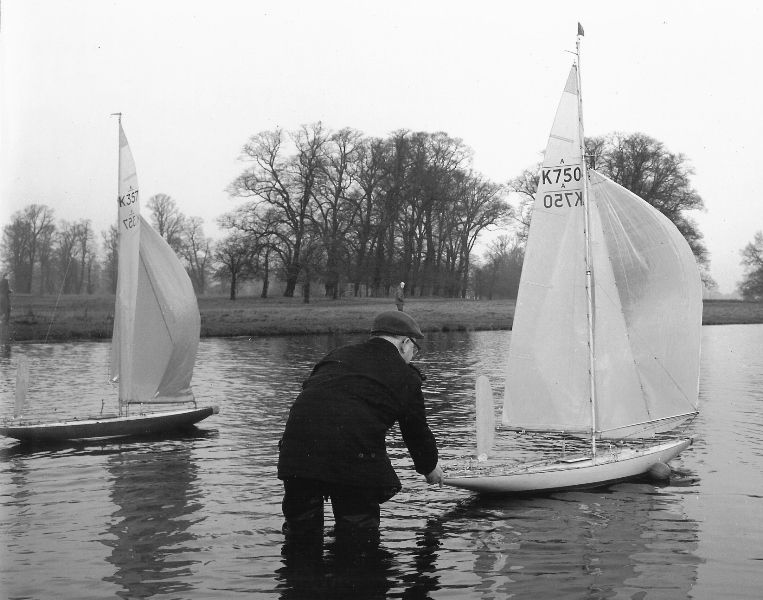
Serica was build by Arthur Levison, another of the great names in British model yachting, The hull would have been built on the bread and butter principle then carved to shape, inside and out. Arthur Levison built many similar hulls in the 1950's, often modifying and developing designs to improve their performance. One of Arthur's other claims to fame is that he carved the figurehead of the Cutty Sark, now preserved in Greenwich.
Serica was not a success as it is thought that Daniels got his calculations wrong and the keel came out significantly too heavy. Under the A class rating formula this meant that it would not be able to carry the optimum amount of sail area and would be uncompetitive.
Arthur Levison built a second hull to the same or slightly modified design but this was never completed and abandoned in its roughly carved state. The reason for this is not clear but it is alleged that it was for an American customer who never took delivery of it. This hull was given to one of Arthur's neighbours and languished there, untouched, until after his death. His widow advertised the hull for sale and the advert was seen by David Bell, who lived nearby and suspected that this might be an Arthur Levison original.
David bought the hull but decided that there was too much work involved for him to complete the build so he passed it on to John Gale. John was also renowned for the quality of his wooden hull construction and had built many classic racing yachts up until his death in 2015. He completed the bare hull of Serica II, including a modified keel to address the over weight issue of the original design. After his death the hull of Serica II was offered for sale by his daughter, but in the confusion, the keel was separated from the hull and lost. In January of this year Elizabeth and I traveled down to London to collect the bare hull and start to plan its completion, 60 years after the original design was done.
More to follow, probably tomorrow.
Gareth
Edited By Gareth Jones on 12/12/2016 20:38:05
Edited By Gareth Jones on 12/12/2016 20:43:00