I've been doing a bit and thinking a lot. I've installed the two winches and the rudder servo. I've also made the 'cheat' fin and a half pattern for the lead bulb in blue foam. It's the lead bulb that's causing me a little headache.
I've made the half pattern from the drawing. It's roughly an aero-dynamic (hydro-dynamic?) shape with a length of 28 cms and a main chord of 7cms. I assume it's circular in section though it isn't stated.
So: I've estimated the average chord is 5cms, hence the volume is given by
pi r^2 x length = 3.142 x 2.5 x 2.5 x 28 = 550 cc. ie a cylinder of radius 2.5cm and length of 28cm
lead has a density of 11.34 gms/cc according to Wikipaedia so the weight of a lead cylinder that size is
11.34 x 550 grams = 6,237 = 6.237 kg = 13.27 lbs!! approx.
That's a lot of lead! Can someone please tell me what I'm doing wrong? Or is the drawing wrong – again?
Here are the fin components. There's only an outline of the fin on the drawing with no clue as to how to make it. I made outlines of the top and bottom of the fin in 3mm ply with a slot at top and bottom to take the 6mm fin blade aft of the 6mm threaded rod. The narrower 6mm part extends downwards to help to locate the lead bulb.
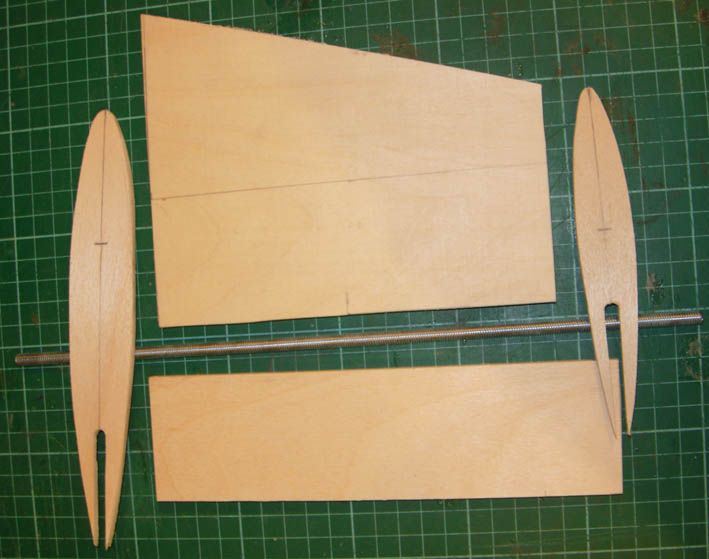
Here are the components being glued together with waterproof PVA. This forms the skeleton of the fin.

The aerofoil shape is done by glueing in slabs of blue foam and sanding to shape using the top and bottom plywood shapes as guides. Blue foam is quite dense and sands well. It's heavier than the more common packing type foam but that's not a problem in a fin. The locating tongue is to the right.
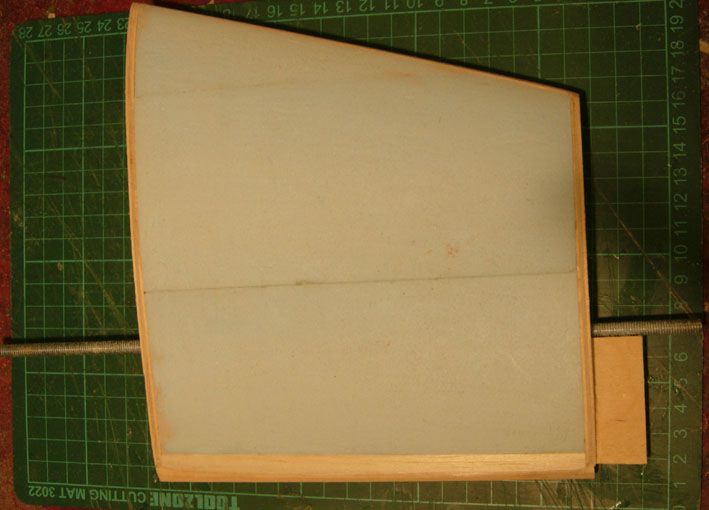
Now we come to the slightly problematical bulb keel. Here's the blue foam half pattern I intend using to make a mold to cast the lead bulb. It's quite accurate to the drawing, though not perfect – after all I made it 
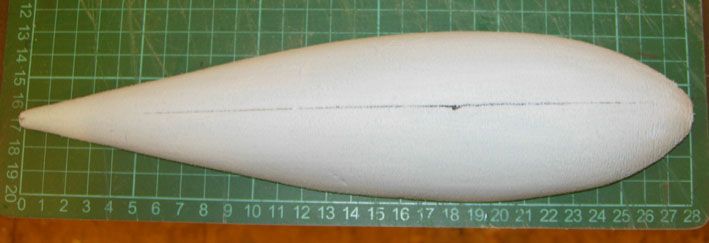
I'd be grateful for any advice on how to make the molds. I've thought of fibreglass (probably cheap polyester resin) or perhaps even plaster of Paris. An easier route could be sand but I've never tried that and I imagine the molten lead just running through the grains of sand.
Mostly I'd be grateful if someone could point out the error in my estimate of the keel weight.
Geoff