Hello Kim
I think this is the Skylark mould box
The box needs to be very strong and at casting time, it should be surrounded by household bricks for safety.
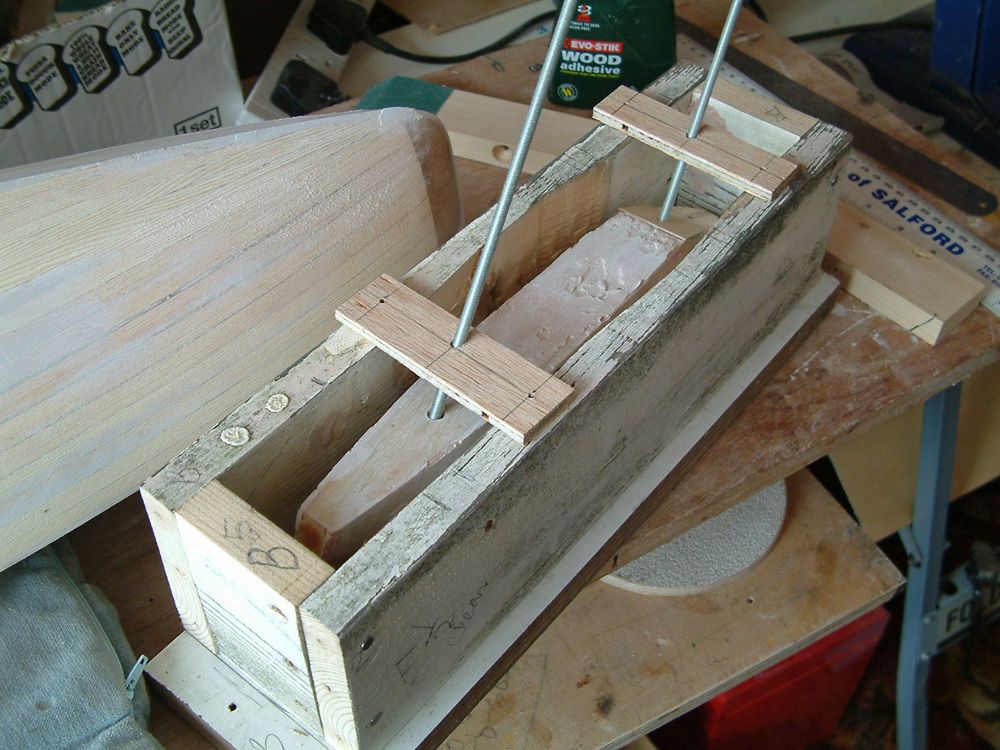
The mould needs to be accurately located and thought given to the retaining rods. In the photo they are shown in the plug. The rods protrude through the plug and into the box base.
Plaster is poured around the greased plug and allowed to set.
The plug and rods are removed and the mould is allowed the dry out completely. The rods have nuts locked together to act as a grip and returned to the mould and finally aligned with the top plates.
Wear protective clothing for the casting process, just in case. Cover your face as much as possible and wear goggles
Use an old pan with two G clamps as handles. I use the kitchen stove for melting the lead….with the door open.
Place the mould on a table outdoors. Make sure access from the stove to the casting table is free from obstructions. Pour the molten lead into the mould. This is normally an anti climax as usually nothing exciting happens!
If you`ve not melted enough lead, just top up the mould a second time
Don`t forget to spoon off the top slag before filling the mould.
When cool, remove the casting by breaking open the plaster etc and fettle the casting to suit the keel.
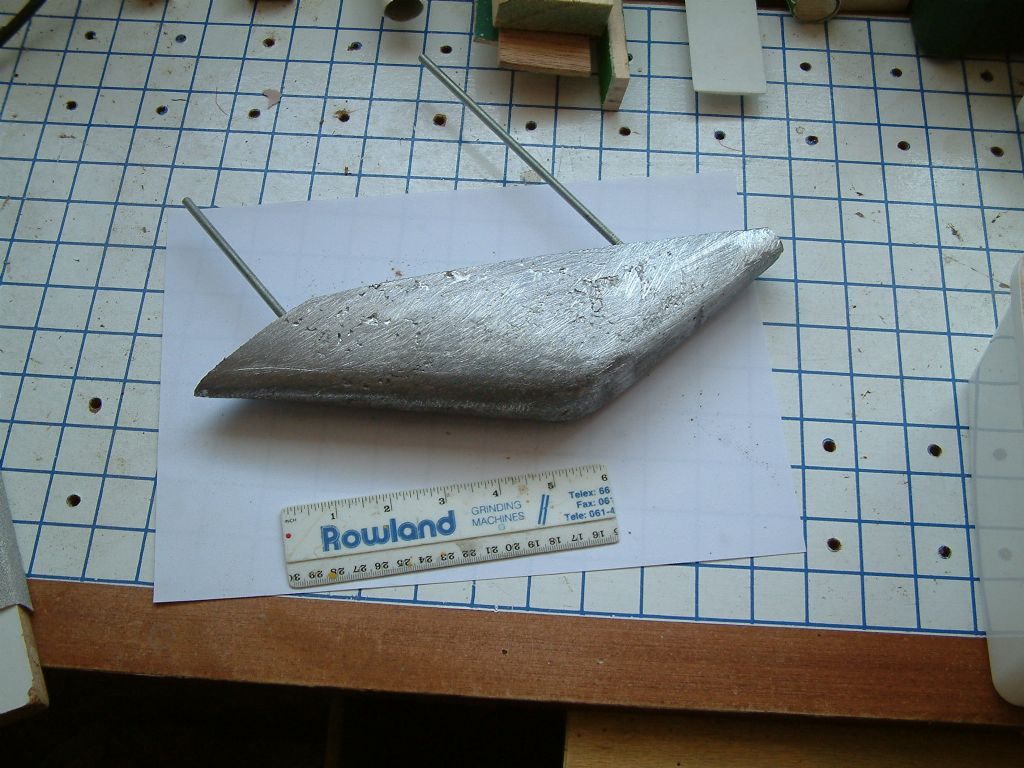
The finished lead insert.
Your questions are welcome
I`ll have a look for more pictures now……BOB