I did start with good intentions but got distracted building a twin engine RC aircraft in the 2018 Mass Build. There is some planking and other techniques that might be of interest. If you want to take a peek click here
Having a good study of the plans and instructions is always a good idea. By doing this I made some early decisions about the build and what I would like to change. I also did some checking around on the internet and some very useful pointers came up and I have cribbed some of those. I will confess when they crop up.
The little oscillating engine is shown connected to the prop shaft with a length of silicone tubing. For one thing the prop shaft and the engine shaft are slightly different sizes with the engine being smaller. The tubing could probably cope with this but the real problem is the alignment.
These little engines are fun to watch and operate but have very little power. The engine is shown mounted flat in the cockpit floor and the prop shaft is at quite a different angle. This will soak up a lot of power and may even stop the engine working properly.
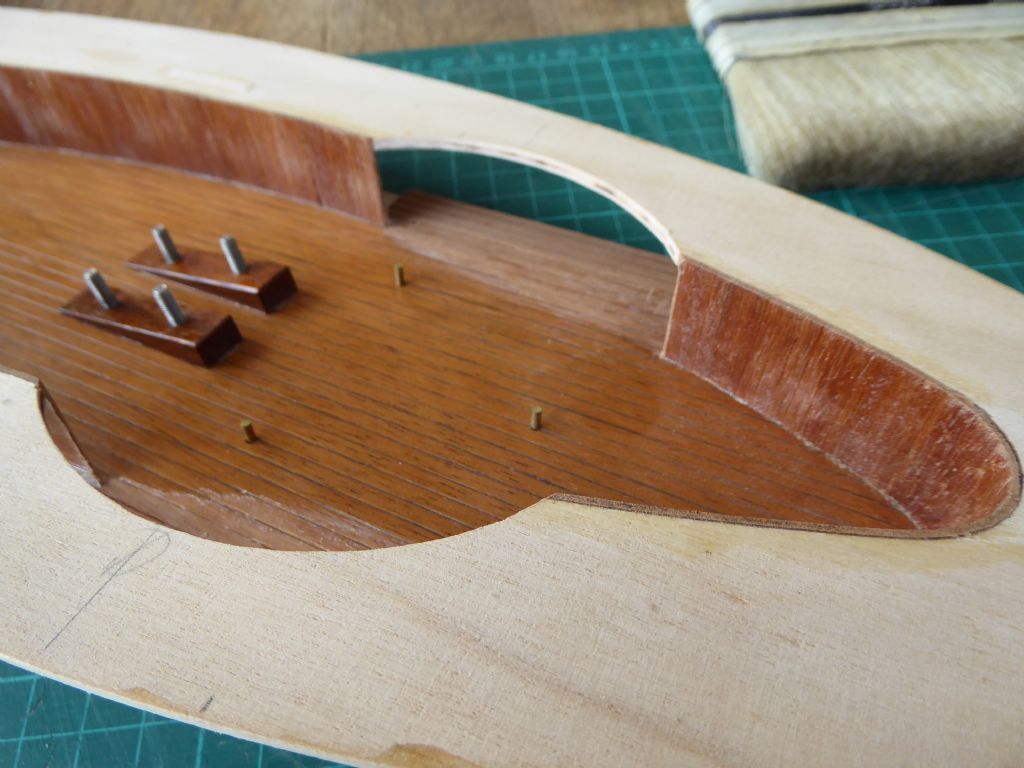
Engine bearers were made in mahogany to bring the engine at the right height and angle to match the propeller shaft. The "bolts" are M3 stainless steel cheese head machine screws inserted from below.
The cut-outs in the coaming sides were cut out after having built them according to the plan. On the internet there was a note about how close the firebox of the boiler came to the woodwork and I am sure they were correct. This was the fix and completed it looks very nice.
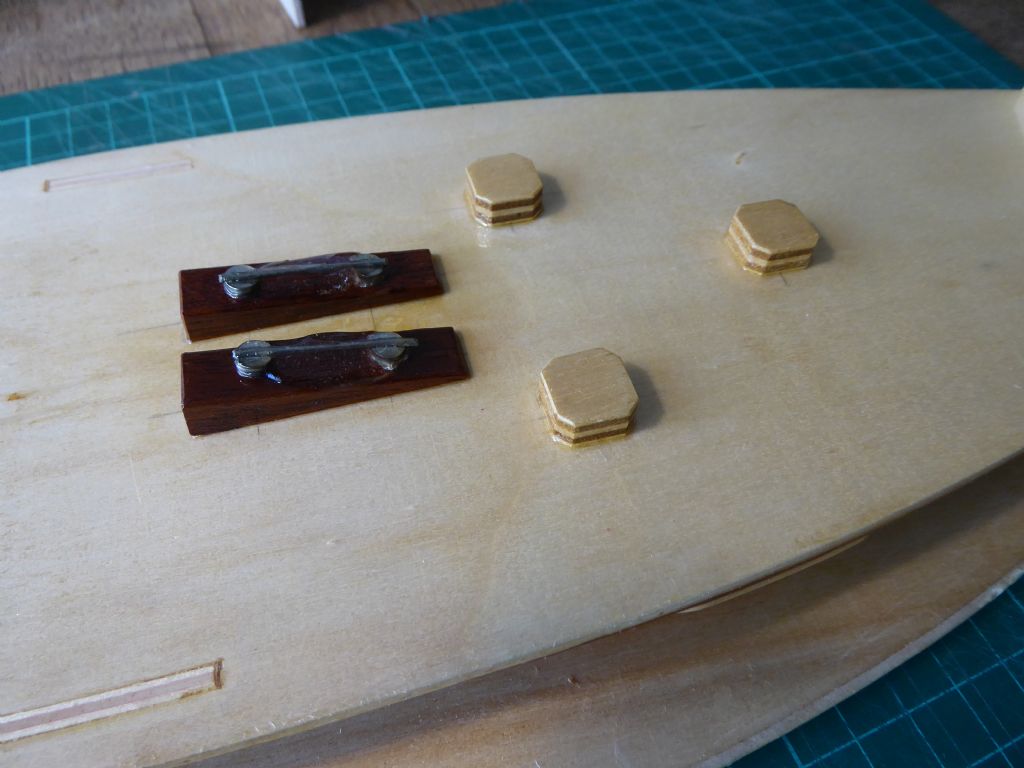
This is the underside of the cockpit sole and show duplicate sections of the bearers glued in place so that the heads of the machine screws have a parallel surface to work on. The slots of the machine screws are lined up to take a short length of piano wire. Don't use soft wire as it is not nearly so strong. The wires were held in place with dollops of epoxy.
The three pads (not on the plan) are to take the pins to locate the boiler. The holes for the pins can now be blind which will stop water leaking through.
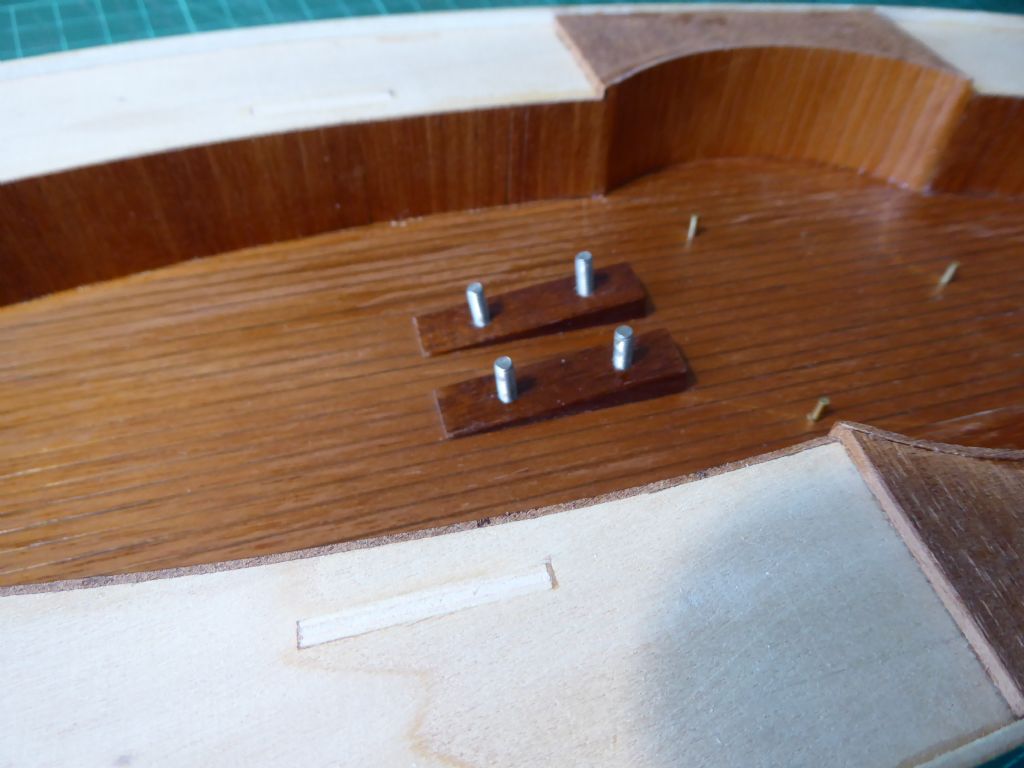
This is what the scalloped out area looked like after re-sheeting and no there is a decent amount of clearance around the firebox.
Tim