JOHN PARKER with some practical advice
This article is intended to provide advice and reassurance, not for those experiencing hair loss, but for those wondering what brushless motors are all about and whether or not they should be using them. It is a practical guide, light and possibly shaky on theory, so if you are an electrical engineer you may wish to put the magazine down this very moment! In my experience, marine modellers are a conservative lot, given more to contemplation of the vagaries of seventeenth century anchor design than the study of the latest technology, and I don’t want to scare anyone away.
Brushed motor operation
Enjoy more Model Boats Magazine reading in the monthly magazine.
Click here to subscribe & save.
Modellers will be aware that the operation of a conventional direct current (i.e. brushed) motor depends on the repulsion and attraction of magnets to provide the forces needed to bring about rotation. A little further thought will show that to keep things moving, one of the interacting magnets will need to have its polarity continually changed, otherwise there will just be a momentary jerk of the shaft and things will come to rest with the magnets facing each other off. The polarity reversal comes from the action of the commutator, a segmented drum that rotates with the motor shaft and thereby is able to receive, from the brushes that press against it, a current of changing polarity to feed to the electromagnet poles of the armature. So the motor requires a commutator to keep it turning, and the commutator is turned by the motor, thus a nice cosy relationship.
This is the technology (amongst other power plants) that has driven our model boats around lakes for over a hundred years. It works, and it works quite well, but there is a downside to that cosy commutator and armature relationship. Chopping and changing the current to the armature in this way causes sparking at the commutator, producing heat, wearing away the brushes, wasting power and interfering with your radio receiver. So, the reason we fit suppression capacitors to a motor is to help quench this sparking. Additionally, power is lost due to the friction of the brushes and design constraints are imposed on the motor that limit its potential.
The alternating current motor, patented by Nikola Tesla as long ago as 1888, does not suffer from these drawbacks. It is able to run directly off alternating current and doesn’t require a commutator to, in effect, make its own. The problem is that the current produced by a battery, whatever its type, is direct current, and the alternating current motor has therefore not been of any interest for portable or battery powered applications until very recently.
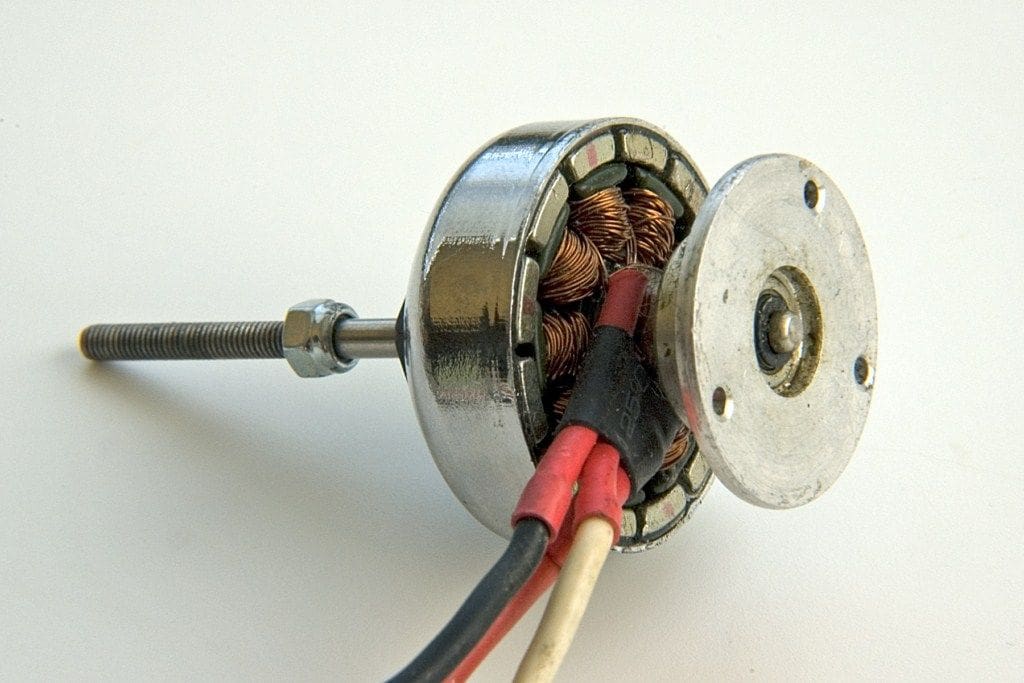
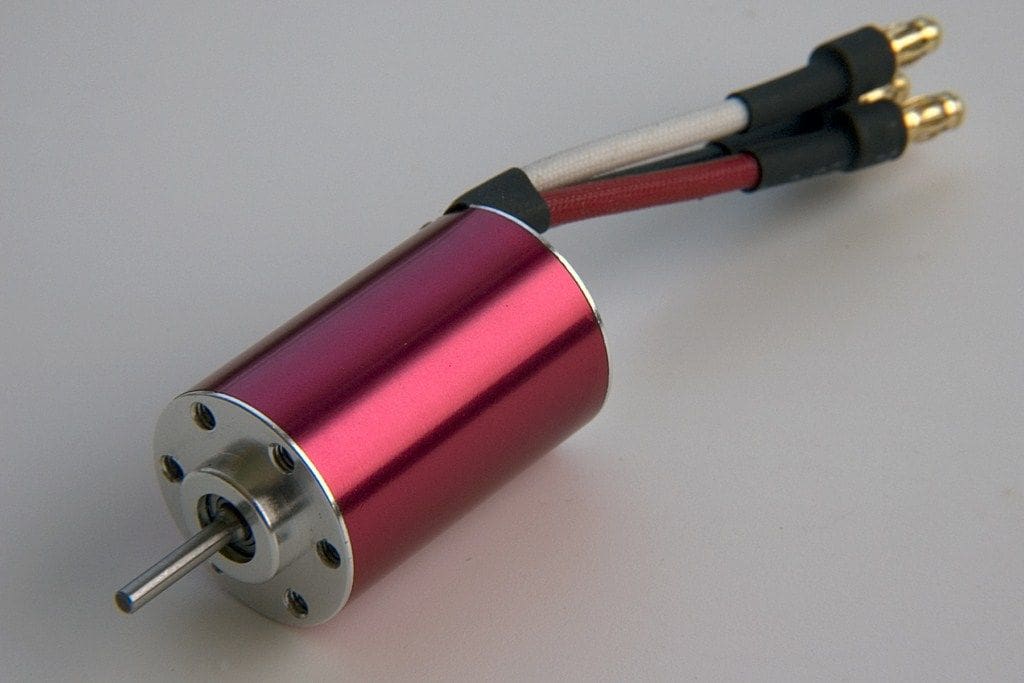
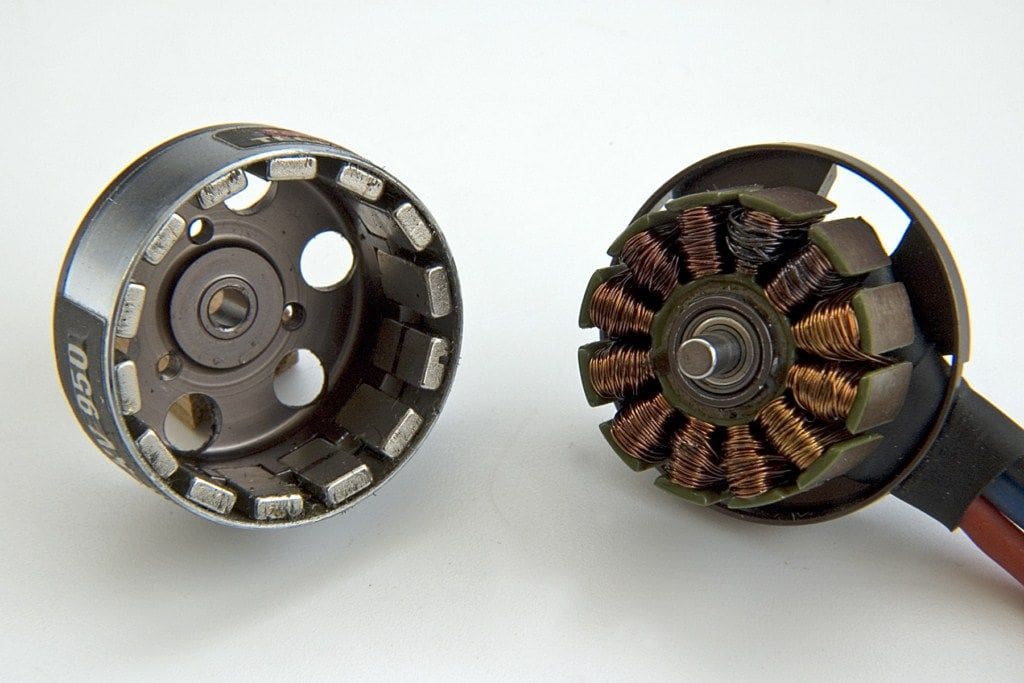


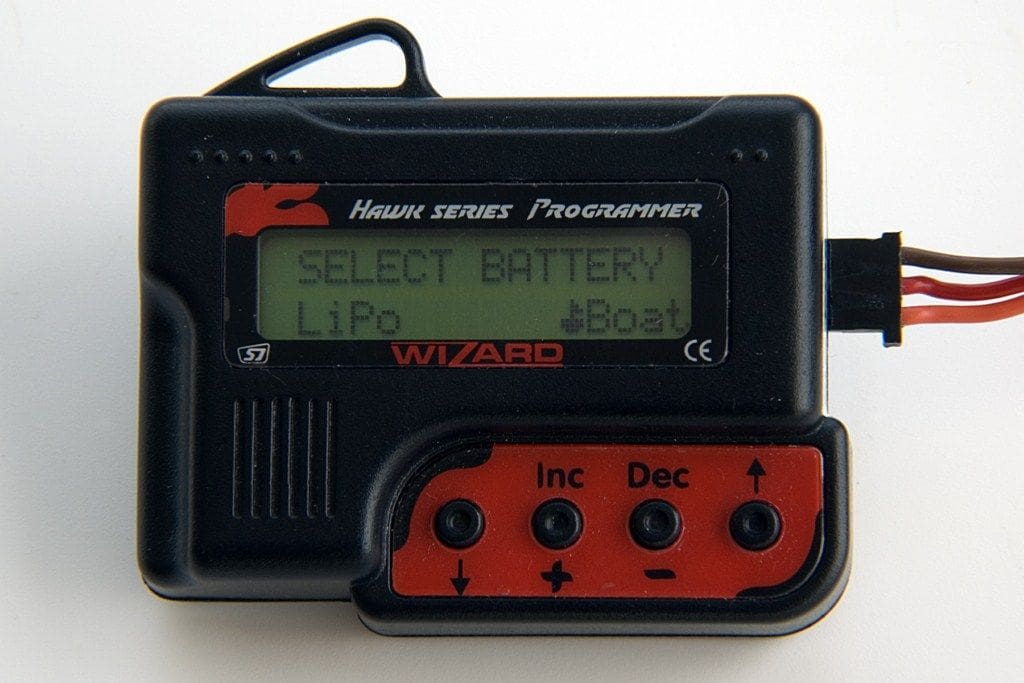
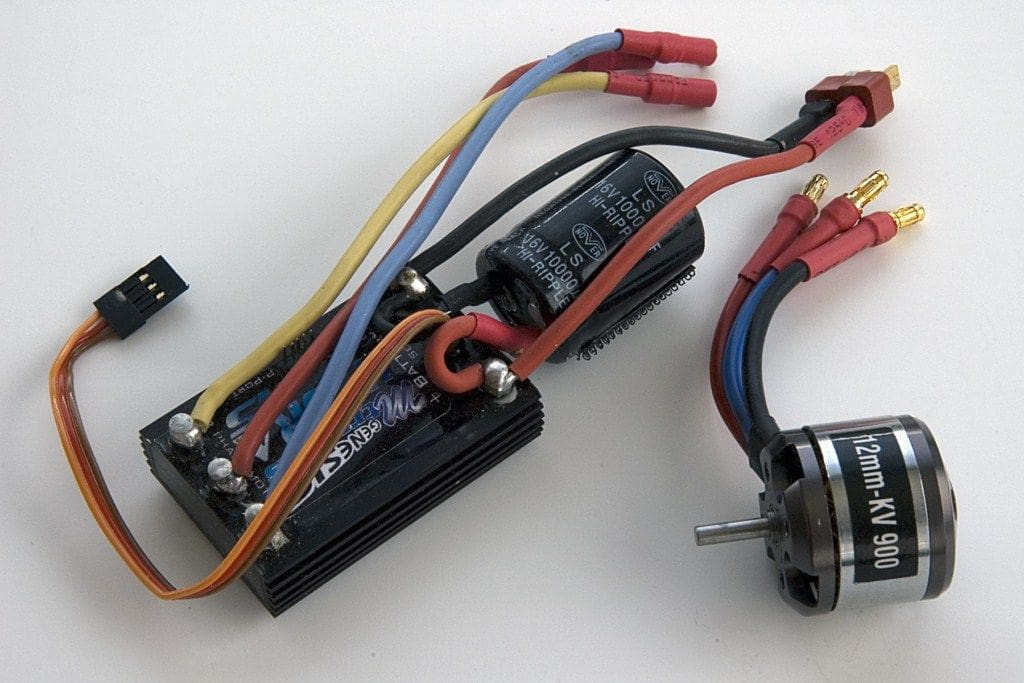
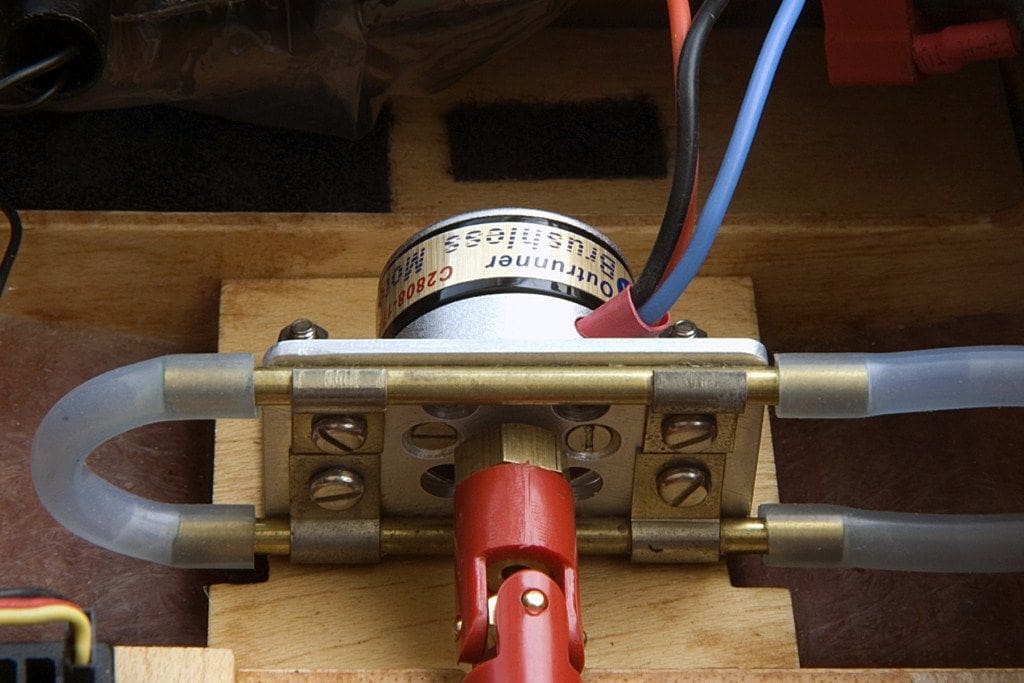
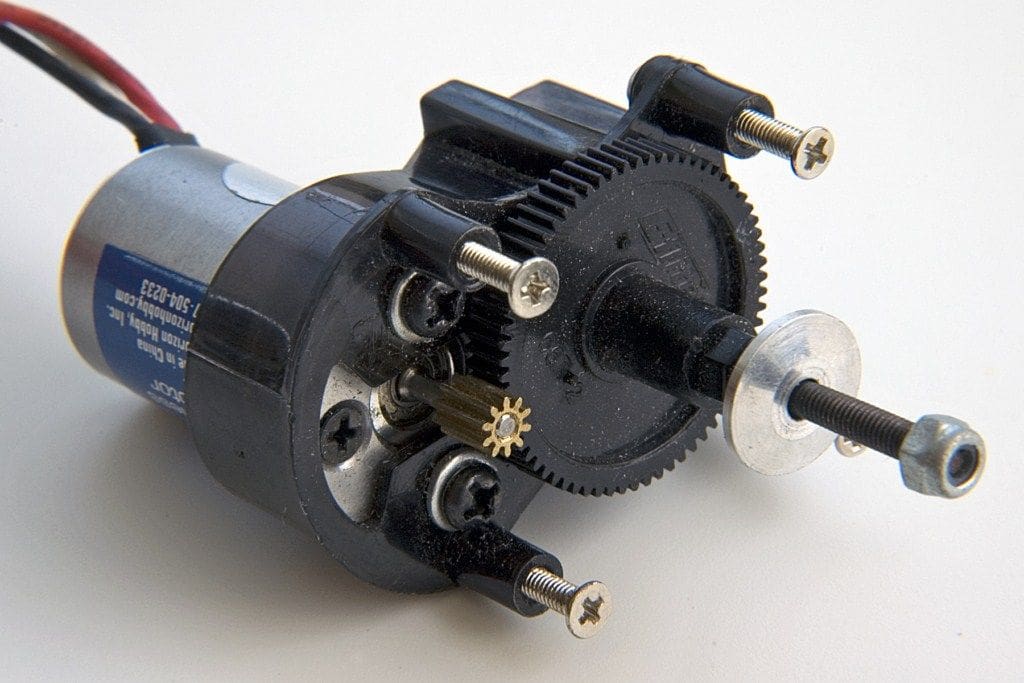
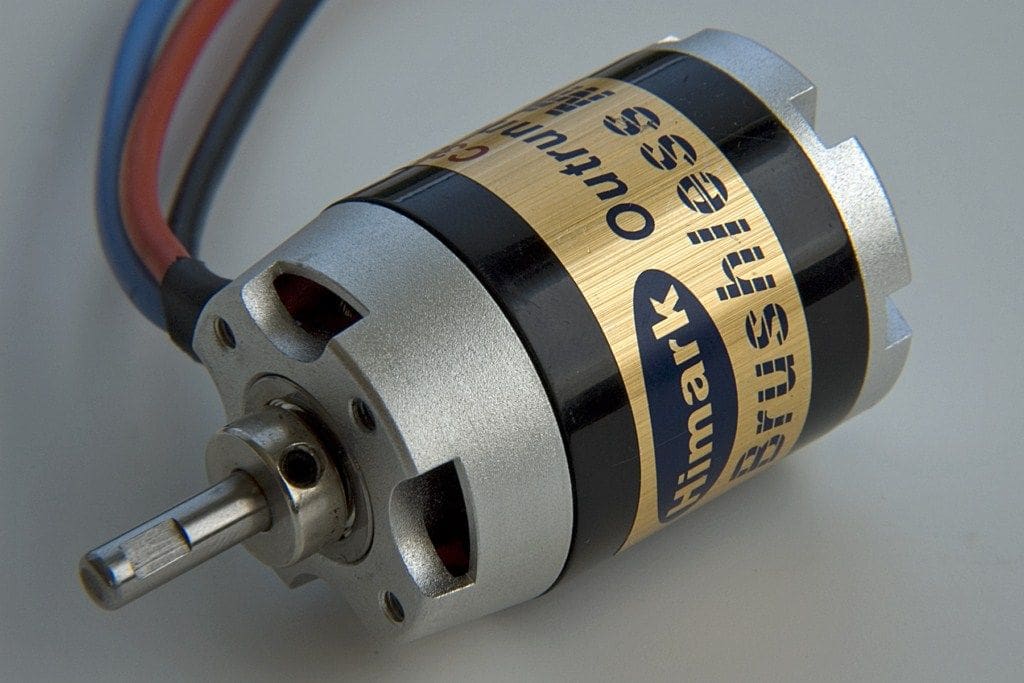
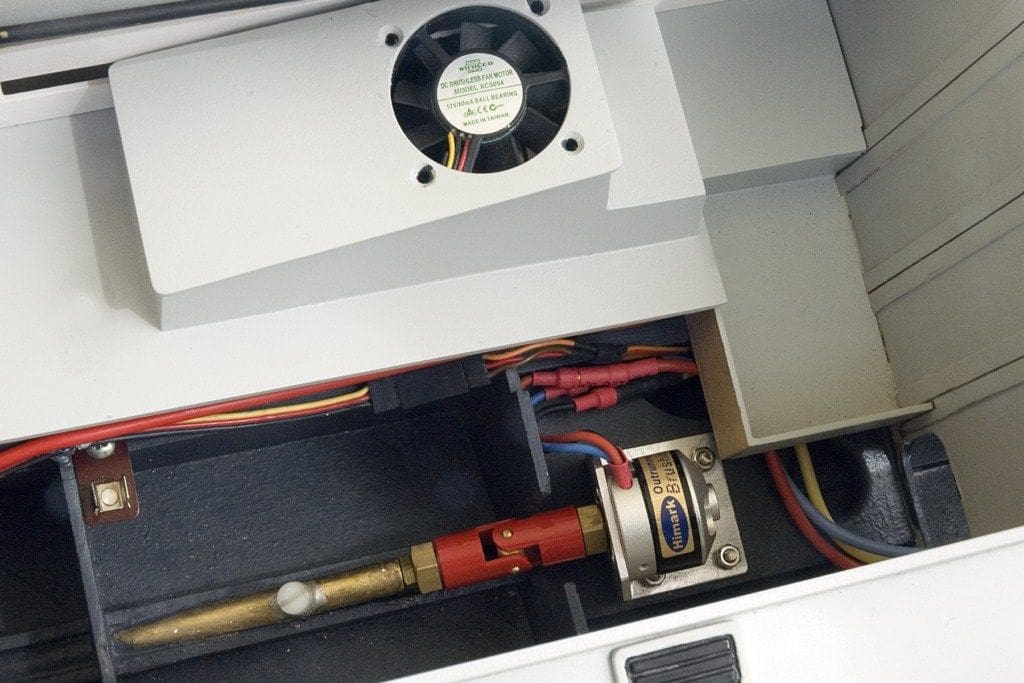
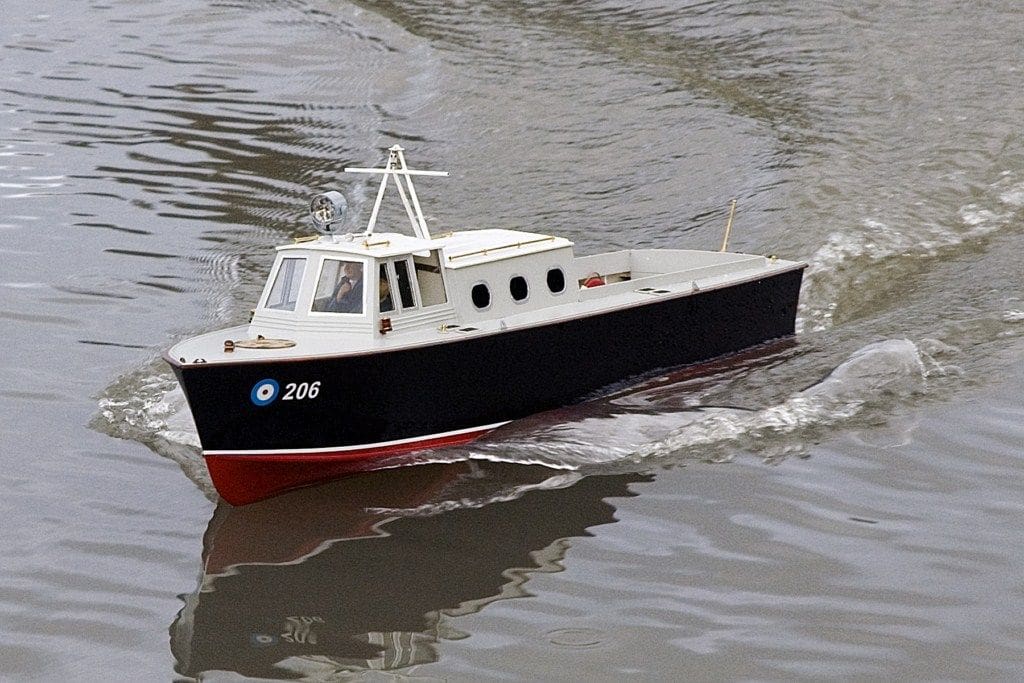
Brushless motor operation
In the last few years there have been incredible advances in electronics, making possible complex circuitry that is nevertheless miniature, low cost and reliable. It has made possible an electronic device that provides the switching function that the commutator of a brushed motor once did, in a process known as electronic commutation. Using this, an alternating current motor fitted with permanent magnets, namely a brushless motor, may be run from the direct current supplied by a battery. In addition, for convenience, this ‘Brushless Motor Controller’ that I will refer to as a BMC, is made to provide us with a throttle function so that we can control the speed of the motor via our radio control receiver. However, there are two main consequences of all of this.
First: The brushless motor is no longer a self-contained device. Without its controller, it is totally incapable of running and is suitable only for use as paperweight (or would be, if it were heavier and better shaped!). That is the downside which is far outweighed by the other fact in that we gain the advantages of an alternating current motor.
Second: Compared to a brushed motor, a brushless motor is more efficient, meaning it makes better use of your precious battery power; is more powerful for a given size or weight, or smaller and lighter for a given power; it requires no maintenance and produces very little radio interference. It may not sound like much put like this, but the improvements can be quite spectacular in practice.
Brushless motor types
Without a need for brushes or a commutator, the electromagnetic windings of a brushless motor are made stationary (the stator) and the permanent magnets made to revolve (the rotor). The wiring connections are permanent and fixed; there is no need to make any electrical connection to revolving parts and two configurations are possible.
If the stator is in the form of a cylinder around the outside of the motor and the rotor spins within it, we get what is known as an ‘Inrunner’. If the stator is in the centre and the rotor spins around it, we get an ‘Outrunner’. Each has its own characteristics.
Inrunners look more like conventional motors, with a fixed cylindrical casing that for example would lend itself to watercooling in the usual way. With a small rotor, they turn at a high rpm.
Outrunners most commonly have a rotating outer casing, with the permanent magnets arranged around the inside of its rim. They turn more slowly and do not readily lend themselves to being watercooled, but because the magnetic interaction occurs at a greater distance from the motor axis, they develop more torque.
Application to marine models
Brushless motors (and lithium batteries) have revolutionised model electric flight, combining internal combustion engine performance with plug-and-play convenience. They are also rapidly taking over from brushed motors in radio controlled vehicles since they were approved by the racing authority ROAR some years ago. Fast electrics are the obvious marine application and here they have been finding many takers, keen to take advantage of the development, production and cost reduction that has come from manufacturers aiming at the model aircraft market. As the market matures there have also come developments aimed specifically at the marine modeller, such as motors with integral watercooling jackets and watercooled controllers.
Any performance-oriented model boat deserves a brushless motor. Here I am thinking of planing craft, which will benefit from the improved power to weight ratio. The appropriate brushless motor might be half the weight and twice the power of a brushed motor. In a scale model, where powerplant weight is not usually an issue, the choice is less clear cut. The ability of an Outrunner brushless motor to drive a large propeller may eliminate the need for a gearbox, saving cost and providing quieter operation. The improved motor efficiency, potentially combined with that of a more efficient larger propeller, will mean longer run times in all models.
There may be other unexpected beneficiaries of brushless motors. In a model submarine, space is very restricted and can result in motor interference problems due to all the components being bunched together. A small brushless motor will eliminate this problem, yield a little more room and drive a larger propeller. However, one disadvantage of brushless motors needs to be kept in mind for scale models. They are unable to be throttled down to as low a speed as a brushed motor, and tend to burst into life when the throttle is opened. This can be noticeable where low speed operation is the norm, such as with a model tug or submarine. Also, with multiple motors, there may be some unevenness in initial response to the throttle, and each motor will definitely require its own BMC (see later).
Battery types
A common misconception is that brushless motors need to be used with lithium batteries. This is false as they will run equally well with any type of battery. A lithium battery/brushless motor combination provides the highest possible performance, but if weight or energy density is not an issue then there is no reason why you shouldn’t use NiMH or even SLA (sealed lead acid) batteries. Just make sure that if you do use a lithium battery, you purchase a lithium-compatible brushless motor controller. This will have a low voltage cut-off to prevent damage of the lithium battery through over discharge (generally set at three volts per cell).
Controller types
In the early days, perhaps just five years ago, almost all brushless motor controllers (BMC’s) available were designed for model aircraft and featured forwards only operation as there is little scope for running model aircraft in reverse. Those that offered reverse were expensive and hard to obtain. Now, with electric race cars making the switch to brushless motors there is a much wider choice of affordable controllers with a reversing function.
The common style of BMC consists of a small circuit board with surface mounted components in a shrink-wrapped plastic sleeve with wires poking out each end. Unless stated otherwise, the assumption is that there will be a generous flow of cooling air courtesy of the large aircraft propeller mounted just in front of it. If you use this type in a boat without any forced cooling, be sure to de-rate it by a factor of two or three. For example, use a 40 amp rating controller for a 15 amp maximum current rating. Run times tend to be longer with a model boat, allowing temperatures to rise higher than with short sprint operation.
A more rugged type of BMC will feature a built-in heat sink, and this would be preferable for a larger model boat. It may then prove quite easy to watercool it by running cooling tubes between the fins of the heat sink. For continuous operation at higher power levels a dedicated watercooled controller is preferable.
Programming a controller
Many BMC’s have parameters that may be selected by the user and are thus referred to as ‘programmable’. The parameters might include the cut-off voltage (for use with lithium batteries), reverse function (enabled or disabled), braking (how quickly the motor responds to cutting the throttle), acceleration (how quickly the motor responds to throttle up), low voltage cut-off type (sudden or gradual) and so on. To enable you to do this using just your transmitter, manufacturers usually provide microscopically small instructions written in pidgin English that require you to interpret a form of Morse Code emitted by your controller in light flashes or beeps whilst you waggle your joystick in the prescribed way. This can be a nightmare, but there are a couple of ways around it.
When I buy a BMC at my local hobby shop, they will offer to set it up for me as I require it and perhaps your hobby store will do the same. Alternatively, most manufacturers offer a programmer to suit their brand of BMC that makes setting up a very simple and quick process. A programmer is not expensive, but only works for one brand and tends to lock you into their product. Provided you are not using a lithium battery, you might prefer to use a non-programmable controller such as the Mtroniks Hydra, which is intended and set-up for model boat use.
Connections
With a brushless motor controller, there are normally three connection streams to be made. For the sake of simplicity, here I am assuming the motor is the far more common ‘sensorless’ type. The signal connection is a flexible ribbon cable with three wires and a standard r/c plug that goes into the throttle channel of your receiver. This will provide power to the receiver via a BEC (Battery Eliminator Circuit) just like a normal electronic speed controller. If you are using a separate receiver battery you will need to cut the red wire or pull its pin from the socket so that your receiver has only one power source.
Two thick leads, usually red and black, are the battery connections and must be fitted with a suitable plug. Double check both the signal and power connections for correct polarity or you will likely do some damage. The three remaining wires need to be fitted with gold plated bullet connectors to match those on the motor wires. It doesn’t matter which of these wires goes where, but if the motor runs in the opposite direction to that required, swap any two of them around. Strange but true!
If your model has more than one brushless motor, then each will require its own controller as you can’t run two motors off the one controller like you can with brushed motors. This is because the controller is using the back-voltage generated by the motor to sense the position of its rotor and provide the correct phasing to drive it and the BMC can’t do this for two motors under varying load conditions.
Choosing a brushless motor
If you’re thinking this has been a straightforward enough topic so far, here is where it all comes apart. The choice of brushless motors, particularly via the internet online, is staggering and grows by the minute. One supplier I looked at has some 370 types listed, from a button-sized one weighing 2.3 grams to one with the power of a 100cc motorcycle engine. Your requirement is likely to lie somewhere between these two extremes, but which is it?
For reasons lost to me, the power of brushless motors is hardly ever quoted and surely this is the most basic parameter we want to know. If the power is quoted, it is often in terms of being equivalent to a certain sized glow plug engine, which is not a problem if you are building a model aeroplane! Your hobby shop will be able to tell you that the Hi-Scream Mega1450 will turn a 9 x 6 inch propeller at 10500rpm and provide 1740gm thrust whilst pulling 27.5 Amps on a 3S LiPo. Please don’t quote me on those numbers, as I just made them up, but you get the point I think.
However, for model boats it’s a very different story. A 40mm propeller? You’ll never get off the ground with that inquiry, so painful though it may be, you will have to pick up some of the lingo.
Brushless motor specifications
Because brushless motors are often used with lithium batteries in model aircraft, their voltage rating may be expressed in terms of multiples of a lithium cell voltage, which is nominally 3.7. So for example, a motor rated at 2S to 3S LiPo has an operating range of 7.4 to 11.1 volts (2 or 3 series connected lithium cells). The rating might also be 6 to 10 cells, referring to NiMH cells of 1.2 volts each or in this case, a 7.2 to 12 volt range.
Next, and peculiar to brushless motors, is their KV rating. This refers to their no-load rpm, expressed in thousands of revolutions per minute, per volt of applied power. As an example, a motor with a KV rating of 2250 will turn at approximately 16200 rpm on a 7.2 volt battery (2250 x 7.2). This is a measure of rpm and not power; a large and powerful motor will likely have a lower KV rating than a tiny motor. If a power rating is quoted, pick a motor with a maximum power of about two to three times that actually required, as the maximum figure is likely to be a short-term one on maximum voltage and with a good cooling air flow.
If, as is common, no power rating is quoted, you will have to work with the quoted current consumption. Try and find a motor whose maximum efficiency current range will yield the sort of power you require. For example, if you know from experience that you need an 80 watt motor and will be using a 7.2v NiMH battery pack, look for one with a maximum efficiency current range of around 9 to 13 amps on 7.2 volts (11 amps x 7.2 volts equals 79.2 Watts). Motors with a higher KV rating will draw more current, not just on load but also when running free.
Physical requirements and type
For most model boats, an Outrunner motor is the preferred choice as it will provide the torque needed to turn a larger propeller. This is usually more efficient and provides a better all-round performance. Due to their rotating cases, water-cooling can be difficult, but one of the photos shows a possible solution provided by cooling the motor mounting plate. The quicker-spinning Inrunners are more suited to fast electrics with light hulls that are able to accelerate to a speed where there will be better propulsive matching to a small fast turning propeller. Of course, there is no reason why an Inrunner (or an Outrunner for that matter) could not be geared down to suit a slower vessel with a large propeller and there are model aircraft gearboxes that might prove suitable for this. Higher powered Inrunner motors are available now with integral watercooling jackets for use in fast electric boats.
Other things to look for are the shaft diameter and length. Does it suit your intended coupling method? The method of mounting, which in the case of some Outrunners can be off either the front or the rear of the motor? When mounting the motor, take care that the mounting screws are no longer than they need be, otherwise they may penetrate the motor innards and cause irreversible damage. All the motors I have seen have had metric threads with M3 being the most common on small to medium motors. An oversized aluminium mounting plate may provide a measure of cooling by acting as a heat sink.
If you are a graduate of the old Taycol school of brushed motors, you will be impressed by the universal use of ball bearings and the precision CNC machined components that go into brushless motors, even the low cost ones. The small Outrunner illustrated, which is the size of a large bottle cap, can equal the power of a 1.3kg Taycol Double Special, so that may give you something to think about.
Examples of conversion
It is all but impossible to provide specific recommendations when upgrading an existing model to brushless power. Not only are there all the usual variables of propeller size and type, battery and so on, but also an almost infinite choice of brushless motors with incomplete or confusing specifications. Some examples of conversions I have carried out might therefore help.
Example One:
A simple lightweight all-balsa fast electric boat originally fine-tuned for best performance on a water-cooled Mabuchi 550 motor, with twin stick 7.2v NiMH battery and two-blade 35E Prop Shop propeller. Fitting a Hi-Mark C2808-950 outrunner motor (the number designates a 28mm diameter motor with 8mm stator length and KV rating of 950) entailed making an adaptor plate for the motor mounting, removing the watercooling and moving the battery well forward to maintain the balance. The overall weight reduction was 160 grams, 15% of the model’s original all-up weight. Performance was slow on the original propeller, but better on a 40mm racing type. Not fully satisfied, I changed the motor for one of the same type but with a KV rating of 1360 and found I now had considerably more speed and a longer run time than with the original set-up. The model was also more manoeuvrable due to its reduced inertia.
Example Two:
A small high-speed midget submarine, originally running a Mabuchi 550 motor on 7.2 volts. A Hi-Mark C2808-1200 was fitted, saving 150 grams which was replaced as ballast on the floor of the engine room providing a significant improvement in static stability. Speed was a little down; the motor needed to drive a larger propeller but I didn’t want to fit one because of the adverse torque reaction on a model such as this. The model therefore awaits fitment of a motor with a higher KV rating (2100 to 2500) and probably an inrunner will be needed to achieve this.
Example Three:
The Dumas utility speedboat, water-cooled 540 motor in unventilated motor box on 7.2 volts. Direct motor change with adaptor plate to Bluebird BLM-8mm KV 950 outrunner. Much improved performance following change to a larger propeller, but uncooled motor burnt out after 30 minutes running on a hot Australian day. Awaits fitment of watercooling to mounting plate and new motor.
Example Four:
This is not a conversion and it is the ST206 Seaplane Tender in 2009 Model Boats Winter Special. This runs fine with forced air cooled Hi-Mark C2808-1360 motors and Prop Shop 1517/3 propellers. The forced air cooling refers to small CPU cooling fans that come on when the throttle is advanced over halfway, which is probably not necessary if you live in a cooler climate than that of Australia. My current model is a classic wooden power yacht and I have reverted to brushed motors, but this is largely because I happened to have two going spare and wanted to prove to my detractors that I am not completely addicted to brushless motors!
What now?
This has only been a brief introduction to the subject of brushless motors. I may stand guilty of over simplification and omission, but have I hope given you some food for thought. You can of course ignore brushless motors and continue to use brushed ones and if you are not building high speed performance craft then you will not be at any great disadvantage. However, brushless motors are not going to go away. I think you will find that manufacturers will not be putting further development into brushed motors for models, so the choice of available types will diminish and that their cost will increase. Inevitably, the hobby shop shelves and website listings will be ever more full of those b***** little brushless things and you will hear them mentioned more and more at the lakeside, sometimes under the breath, but more often in amazement. So, here’s a suggestion if this all makes you feel a little uneasy.
Buy yourself a small brushless motor and controller. They can be bought for as little as US$25 the pair (or the equivalent elsewhere in the world) if you get the type used in small aircraft models and charge it to your research and development account, connect them up and experiment with them. Try and relate the specifications with what you are seeing and perhaps measuring on the test bench. You will thus learn a lot and feel more comfortable with the technology. Then put them in a simple airboat or fast electric model and have some fun, but don’t blame me if you get hooked!