COLIN BISHOP visits this well known British kit manufacturer
Jackie and Lawrie White – the heart of The Model Slipway
I don’t suppose any regular reader of this magazine will be unaware of the extensive range of kits offered by the Model Slipway. Since the establishment of the company in 1989 they have established an enviable reputation for producing attractive, colourful and ‘chunky’ model boat kits to a high standard and with exemplary after sales service. So I was keen to see what lies behind the regular advertisements when I visited Lawrie and Jackie White at their manufacturing facility in Barnsley, Yorkshire.
Enjoy more Model Boats Magazine reading in the monthly magazine.
Click here to subscribe & save.
My first impression on seeing the well laid out factory unit that the company operates from was: ‘How do they manage all this between the two of them plus one part timer who moulds the GRP hulls?’ However, it swiftly became clear that Lawrie and Jackie are a very efficient and well organised team. Lawrie’s extensive all round engineering and technical knowledge enables him to turn his hand to almost anything, while Jackie’s is the business brain handling administration, accounting, advertising, website and packaging, plus a lot else besides.
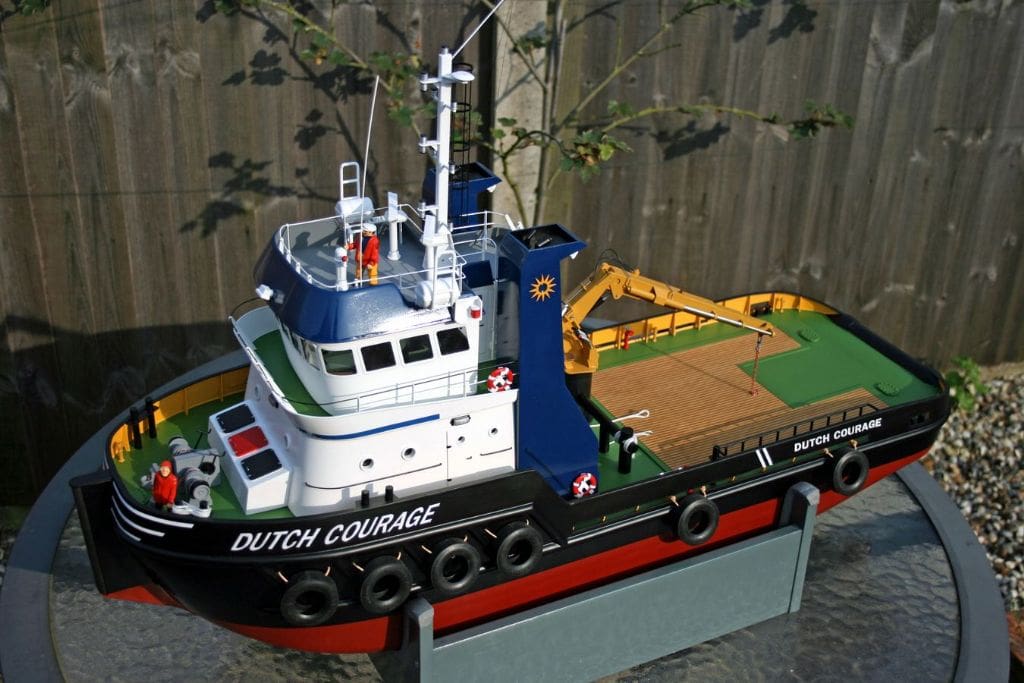
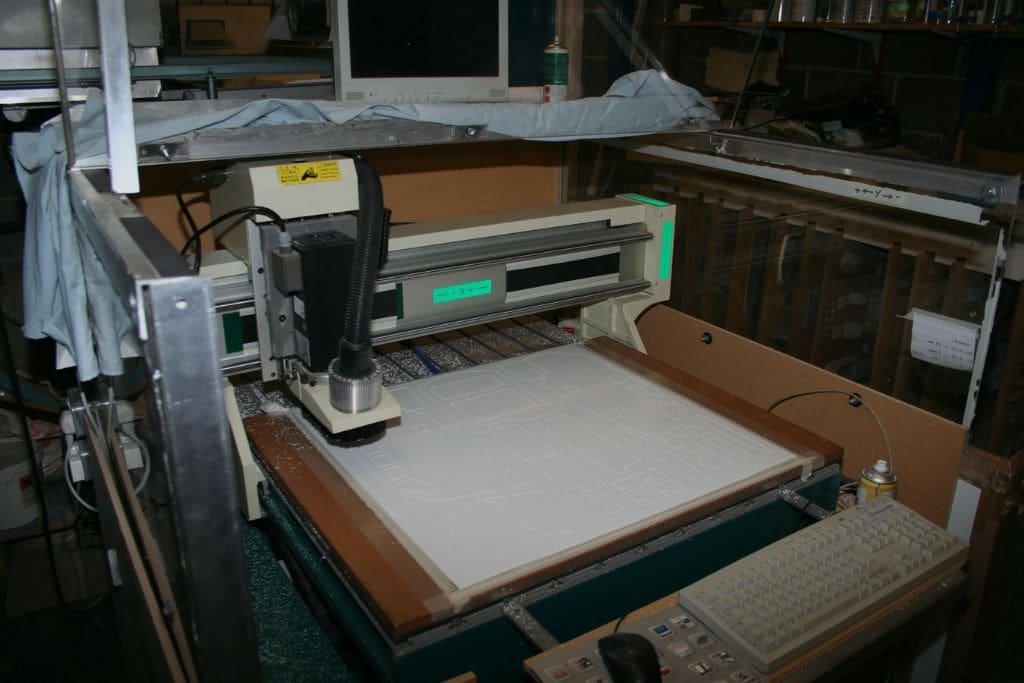
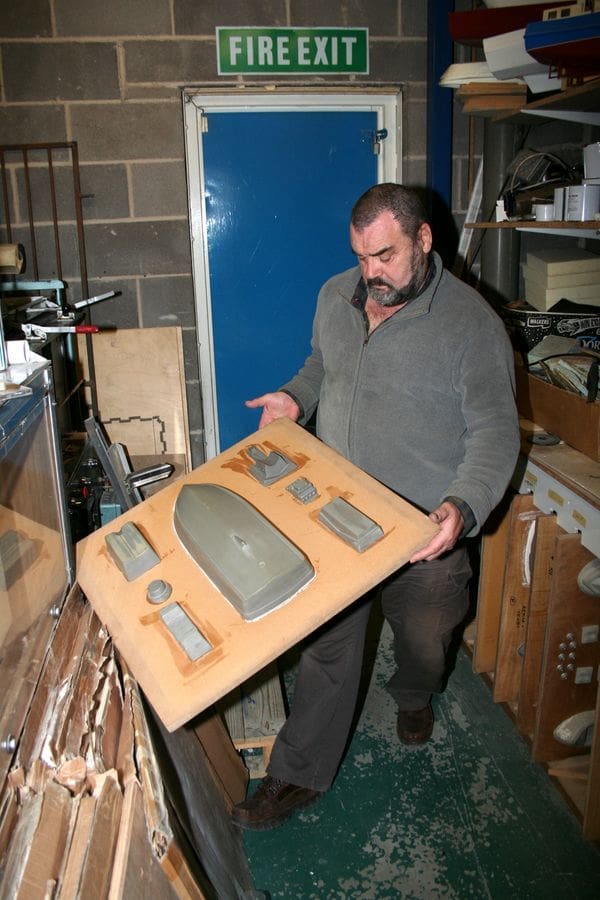
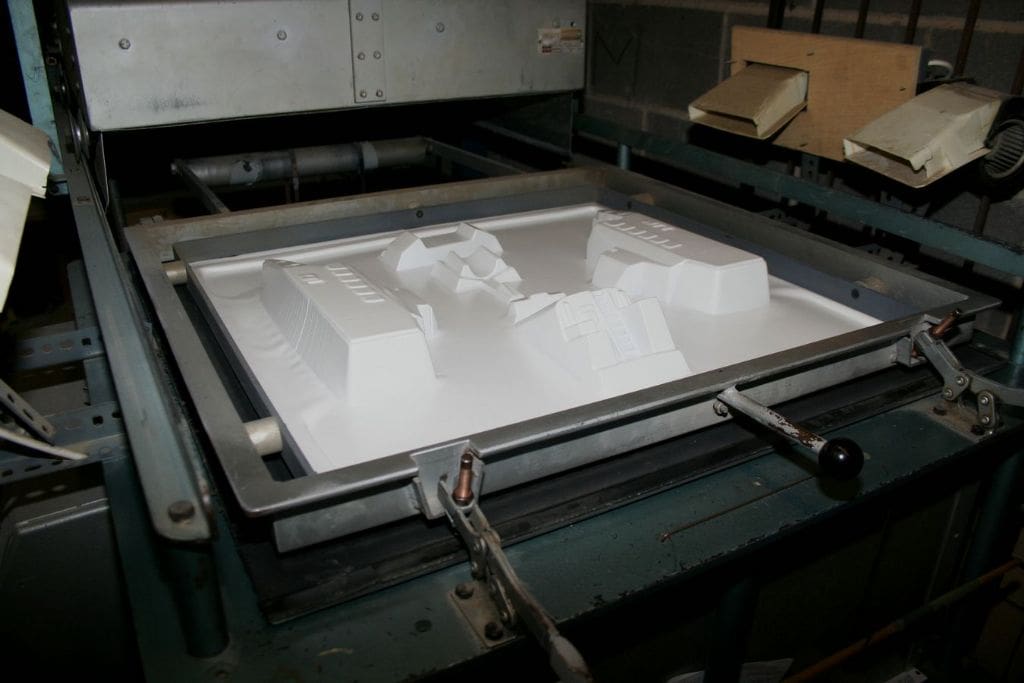
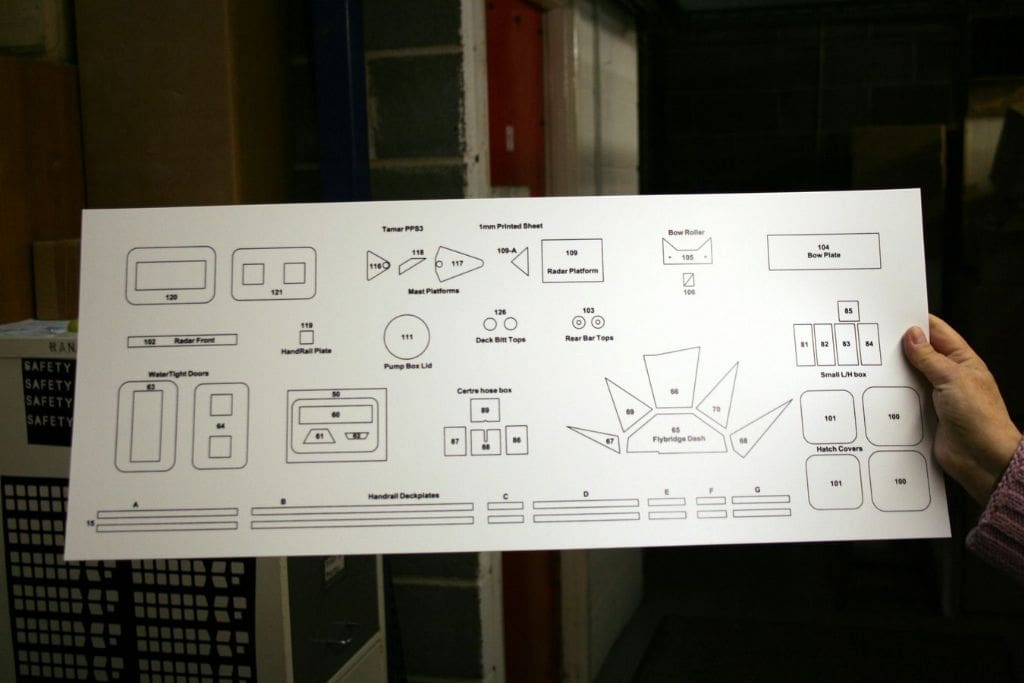
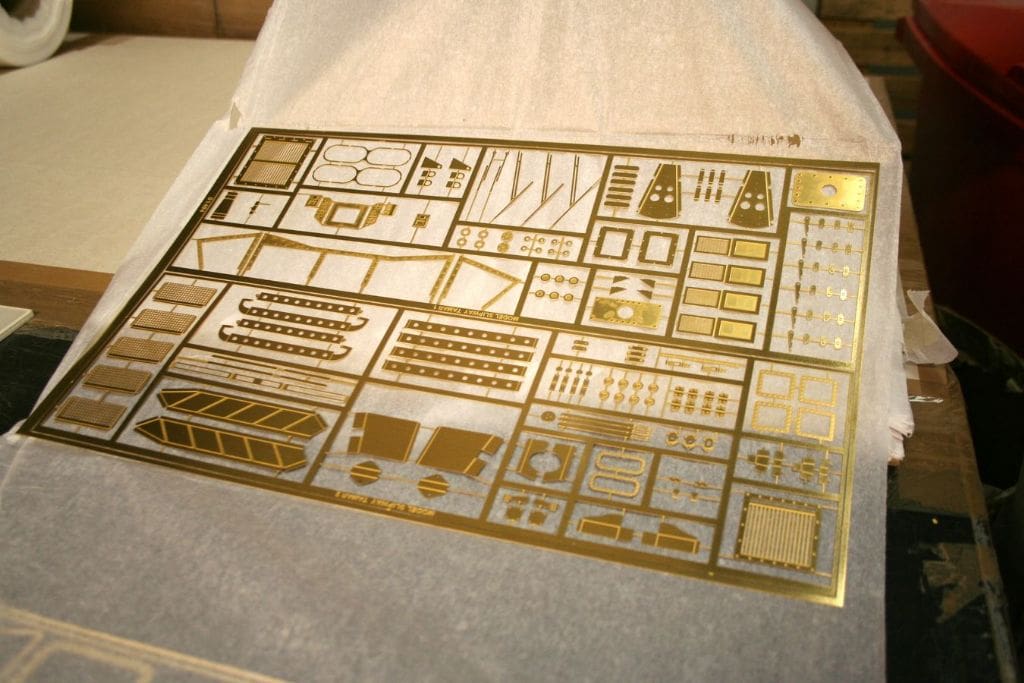
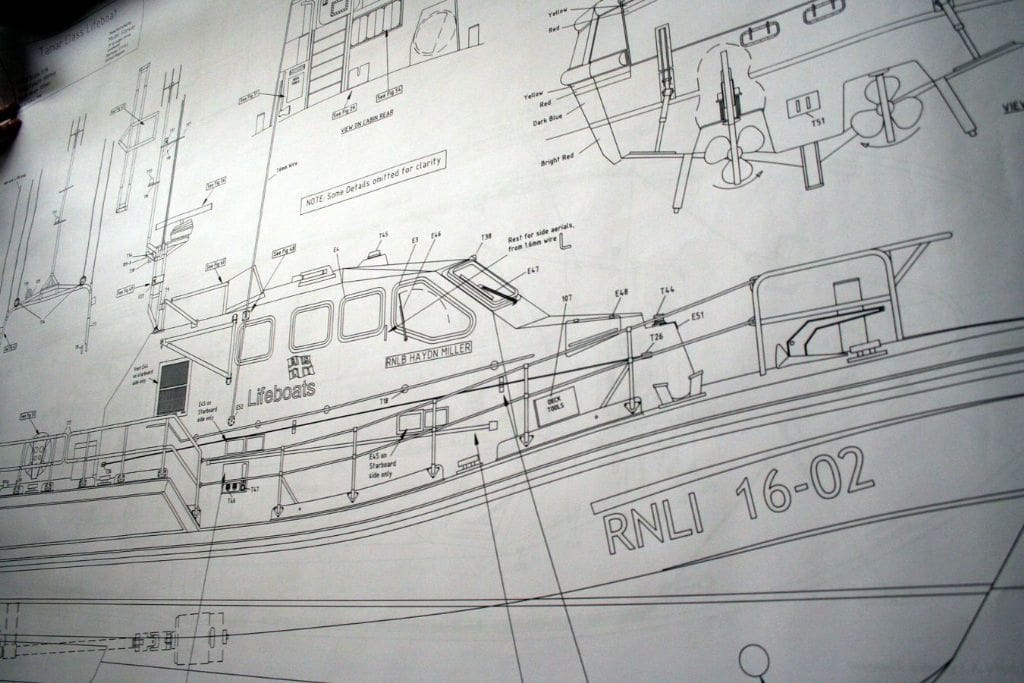
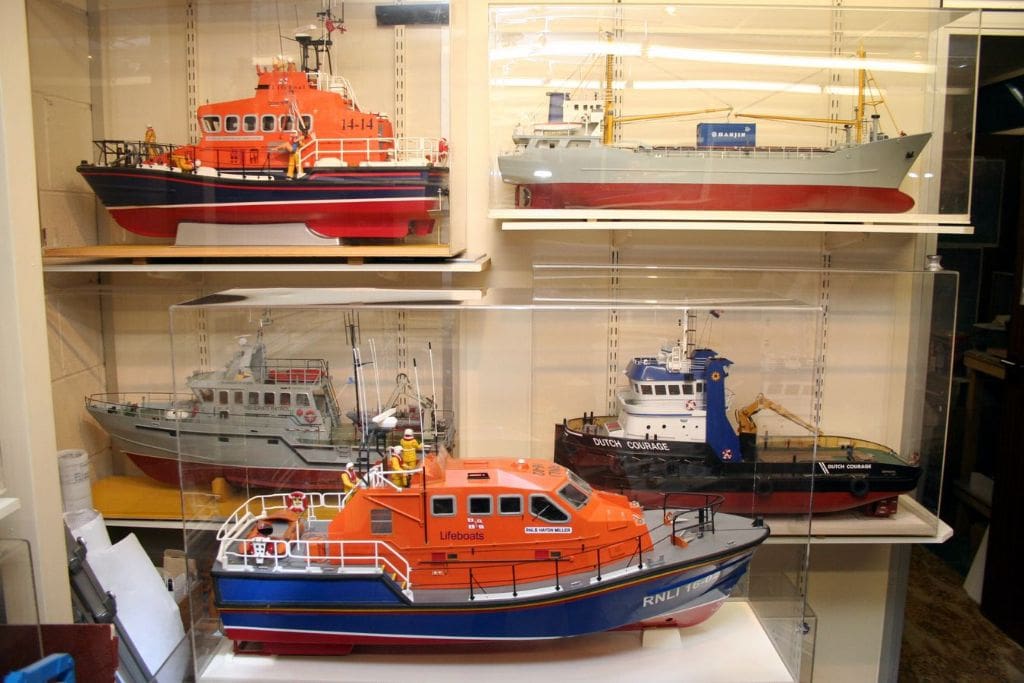
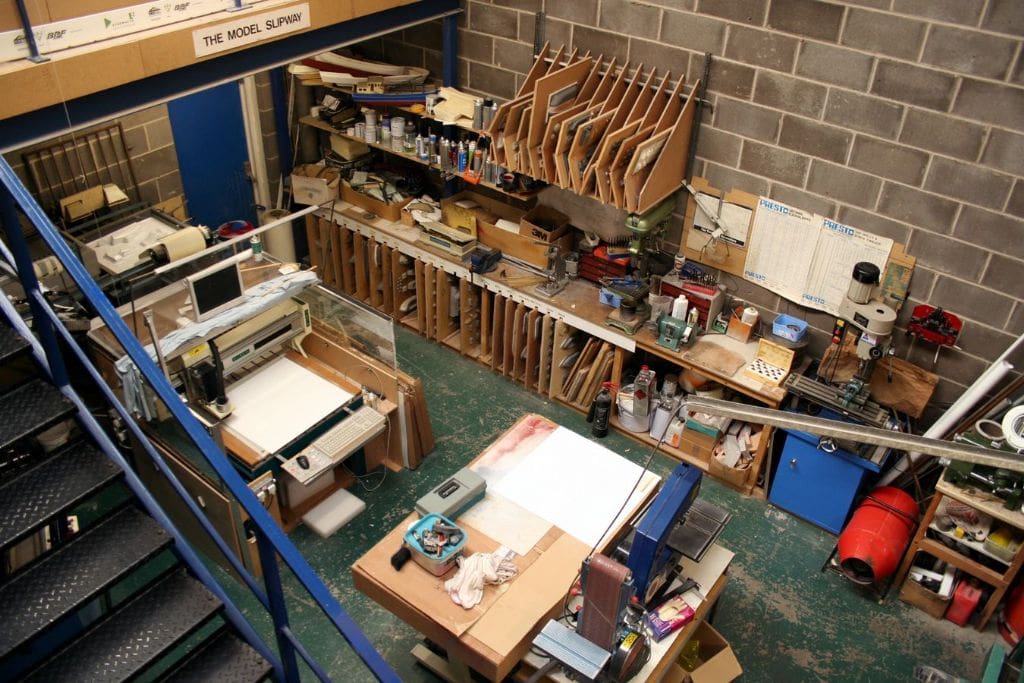
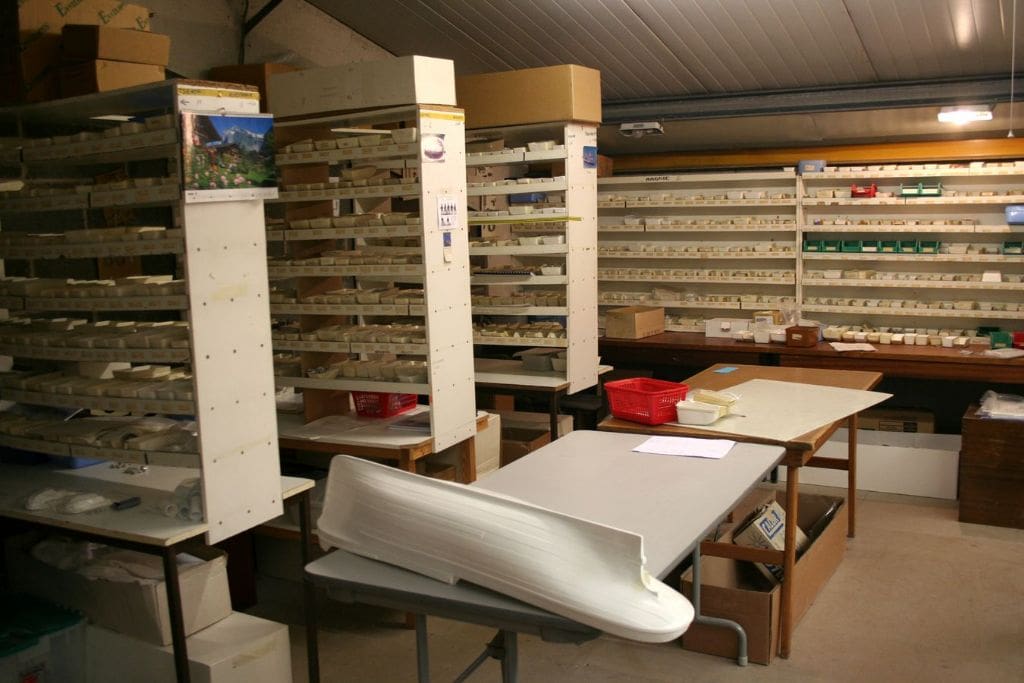
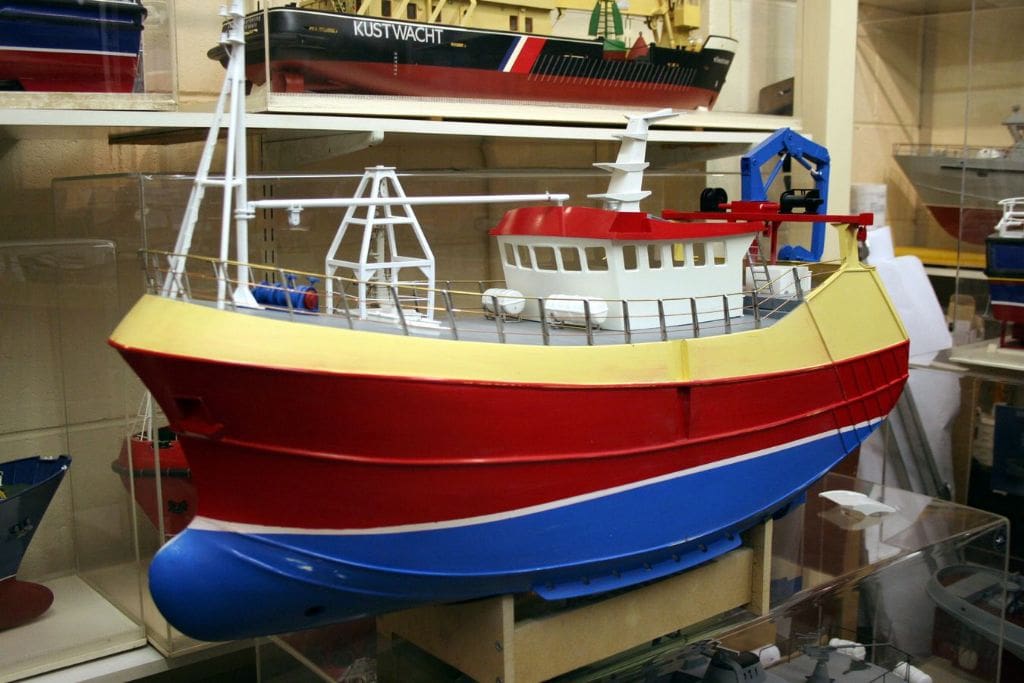
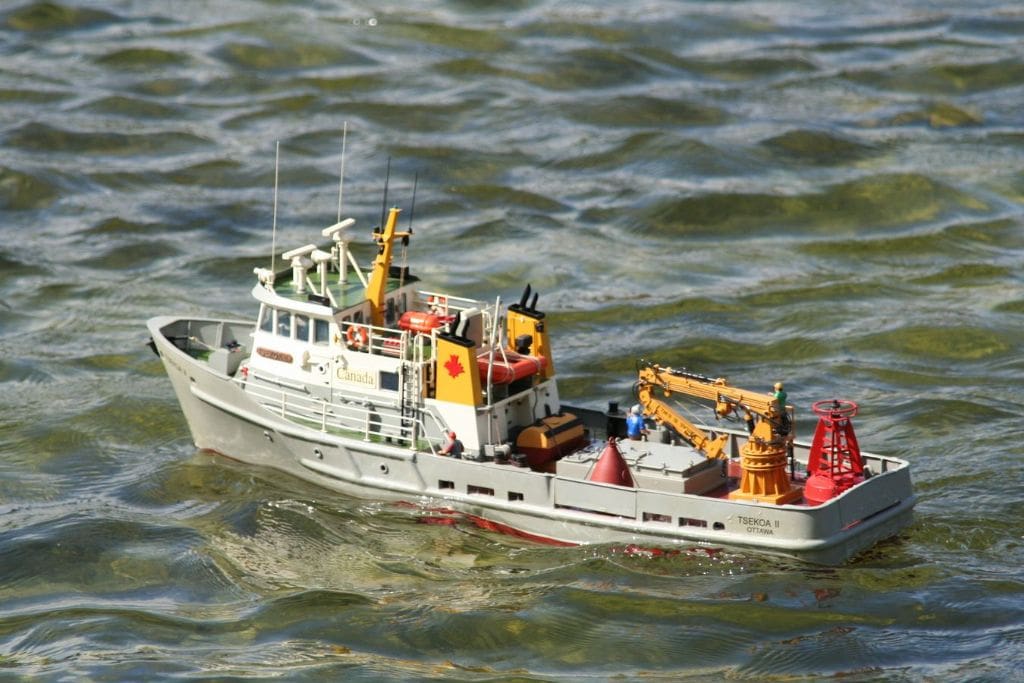
Choosing the prototype
Before diving into the production technicalities I asked Lawrie how he comes to choose the prototypes selected for development into kits. He replied that he follows his instincts and if the original vessel appeals to him then there is probably a viable market for it. There are of course practical considerations as well. Customers like models they can fit into a standard car and can be managed and launched by one person. Basic stability is also important, while building to a reasonably large scale means that most of the fittings on the original ship can be replicated on the model and are large enough to be robust when constructing the model and in practical use. There are less obvious factors too, such as the need for the box to fit in a standard international cargo pallet otherwise the shipping costs could approach the value of the kit itself – something which is very important given that around 80% of production is exported, mainly to Germany and the USA.
The production process
With the exception of fibreglassing work, just about everything is done on site. A new kit can take between two and three years to bring to market and as you might expect, it all starts off with the drawings. Many of the Model Slipway range are vessels which have been recently constructed and permission is needed from the owners before work can begin. The main source material will be general arrangement plans of the full size vessel from which Lawrie will develop a CAD (Computer Aided Design) file which will be used as the source data for the kit in order to program the computerised printing and routing machines which actually produce the main kit components. Hull lines drawings enable Lawrie to construct a plug which is used to make the master hull moulds from which the GRP hulls are laid up or the styrene ones moulded.
The initial CAD files are used to develop the individual kit parts such as superstructure elements and deck constructions. These can then be tested using the CNC Router to cut out the pieces to check that they fit together properly. If errors are found then adjustments are made until Lawrie is satisfied that there is a good fit. This method also means that if anything does slip through the net and is picked up by the customer, then it is relatively easy to make appropriate corrections in future production and send updated parts to existing customers on request although Lawrie says that this only happens very occasionally as the development process is extremely thorough.
The Model Slipway range makes extensive use of styrene mouldings and the plugs for these are mounted on standard sized boards combining components that are normally required together. The boards can then be located in the moulding machine, a styrene sheet placed over the top and the heat turned on! When the plastic is sufficiently supple the air beneath the plugs is sucked out causing a partial vacuum and the styrene immediately moulds itself around the plugs. Cold air is then blown in from above to cool the plastic and the sheet with its moulded components can be extracted and cut up as required.
As with many kits these days, the majority of the fittings are of white metal. While this is sometimes not seen as being the ideal material for certain items, for most small manufacturers it is the only practical option as production runs could never justify the huge cost of investing in injection moulding equipment. For the majority of fittings in the Model Slipway range, white metal is perfectly okay and never less than adequate. Lawrie has gone to a lot of trouble to find an alloy mix which will preserve fine detail on smaller fittings without exhibiting shrinkage on larger items as the metal cools. Builders who wish to customise their models can always substitute alternatives from the after market if they wish, but quality control by Model Slipway is very good though. Master fittings are typically made from hard brass and used to produce a number of secondary masters in white metal which are in turn used to make the production masters. Then the primary and secondary masters are stored safely away so that if the production master moulds begin to wear, new ones can be made with the assurance that they will exactly replicate the originals. The production fittings are inspected no less than three times before they find their way into the kit box. If any rogue items should make it through this scrutiny then Model Slipway will replace it on request – and really you can’t expect better than that!
As I have noted before on these Trader Visits, small manufacturers need to work smarter to stay competitive, matching production to demand, and Lawrie and Jackie have this down to a fine art with some very clever and ingenious attention to detail. The computerised production process means that there is no need to have racks full of unsold kits in storage tying up both capital and space. The CNC router can produce a set of partially cut styrene superstructure components for a kit in just a few minutes using the CAD master instructions so all that has to be kept in stock are the basic styrene sheets. These are also used to make the styrene mouldings described above and a set of standard sheet sizes meets all production requirements. A selection of coloured sheets is kept for production of the Club 500 racers.
Fittings are cast or moulded in batches and stored in hundreds of labelled bins so there is always a working stock in hand. As bin contents start to run low they are replenished during the next manufacturing session.
The instructions!
These are a vital, but sometimes rather neglected part of any kit and can make or almost literally break a model. Model Slipway are well known for their comprehensive and clear instructions which continually evolve in response to customer feedback. The new Tamar lifeboat instruction book for example, has no less than 75 pages. Each kit comes with a detailed full sized plan with all the fittings and components clearly labelled. This is backed up by an illustrated construction manual. With many kits, you will often find that the text and the illustrations are separate, but the policy in Model Slipway is now to use the CAD facilities to associate 3D drawings with the relevant text which makes it much easier for builders to understand just how the kit goes together and reduces the likelihood of mistakes being made.
Website
The company have a clearly set out and extensive web site: www.modelslipway.com which showcases their products and customer builds where you will find lots of information about both the kits and their full size prototypes together with a selection of reviews published in the modelling press. There is also a very useful tie in with ACTion R/C Electronics (see MB May 2009 issue) who have produced detailed r/c and power wiring diagrams for most of the Model Slipway range using ACTion products, although much of the information can be adapted to the requirements of the builder. Guidance is given on the recommended skill levels for each model together with practical hints and tips on construction. Kits are available in the UK direct by mail order or from major retailers advertising in Model Boats.
Afterword
I have reported on a number of traders in this series and in each case I have been impressed with what I have found. All have been fine examples of how to run a successful operation and deserve to succeed in their particular line of business. Model Slipway is no exception to this rule and in many respects go that extra mile, fully justifying the enviable reputation they have built up for quality, attention to detail and customer satisfaction. I would like to thank Jackie and Lawrie for their time in showing me around and explaining just what lies behind the scenes of their attractive and deservedly successful range of kits.
Contact Information
Mailing address: Model Slipway, 77 Arundell Drive, Lundwood, Barnsley, South Yorkshire, S71 5LE, United Kingdom.
The factory is at: Unit 8, Grange Lane Industrial Estate, Carrwood Road, Stairfoot, Barnsley S71 5AS, U.K. (Monday to Friday 7am – 3pm).
Phone & Fax: UK: 01226 770008, International: +44 1226 770008,
Website: http://www.modelslipway.com/
Email: [email protected]